optical sorting machine for Sleeves: A Comprehensive Guide
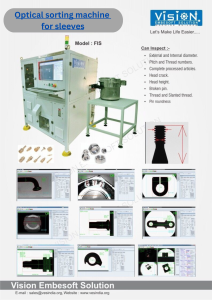
Introduction
Sleeves, the unsung heroes of countless industries, require impeccable quality to ensure structural integrity and product performance. To achieve this, advanced inspection and sorting systems are essential. This blog delves into the world of Sleeves inspection sorting machines, exploring their functions, benefits, and the technology behind them.
Understanding the Need for Sleeves Inspection
Sleeves, such as wing nuts, bolts, nuts, and Sleeves, undergo rigorous manufacturing processes. However, imperfections can arise, impacting product quality and safety. Traditional manual inspection methods are time-consuming, prone to errors, and unable to handle high-volume production. Here’s where automated Sleeves sorting machines shine.
How Sleeves Inspection Sorting Machines Work
Leveraging machine vision and advanced algorithms, these machines meticulously examine each Sleeves for defects like:
- Dimensional inaccuracies
- Surface imperfections
- Thread damage
- Material flaws
Once inspected, Sleeves are categorized and sorted based on criteria like:
- Size
- Shape
- Material
- Grade
- Other specified parameters
This automated process ensures unmatched precision and speed, significantly enhancing overall efficiency.
Sleeves Inspection Sorting System: A Comprehensive Quality Control Solution
A Sleeves Inspection Sorting System is a sophisticated piece of equipment designed to ensure the highest quality standards in Sleeves production. This advanced technology can meticulously inspect various Sleeves attributes, guaranteeing precision and reliability.
Key Inspection Capabilities:
- Dimensional Accuracy: Precise measurement of external and internal diameter, pitch detail, thread detail, and length.
- Thread Quality: Detection of slanted, reverse, or incomplete threads, ensuring thread integrity.
- A Sleeves Inspection Sorting System is a sophisticated piece of equipment designed to ensure the highest quality standards in Sleeves production. This advanced technology can meticulously inspect various Sleeves attributes, guaranteeing precision and reliability. Geometry: Evaluation of pin roundness, chamfer, and head shape (top, bottom, and side inspection).
- Defect Identification: Advanced algorithms to identify defects such as head cracks, broken pins, and other anomalies.
- Surface Quality: Inspection for scratches, burrs, and other surface imperfections.
- Presence and Absence Detection: Verification of all Sleeves components.
- Automated Vision Testing: Real-time image analysis for comprehensive inspection.
- Pattern Matching: Identification of correct Sleeves patterns and orientations.
- Robot Integration: Vision-guided robots for automated handling and sorting.
- Part Verification: Comprehensive assessment of Sleeves orientation, function, dimensions, and finished part features.
- Color Verification: Accurate color matching for coated Sleeves.
- Barcode Reading and Traceability: Efficient tracking of Sleeves throughout the production process.
By incorporating these capabilities, Sleeves Inspection Sorting Systems play a crucial role in maintaining product quality, reducing defects, and optimizing production efficiency.
Key Components of a Sleeves Inspection Sorting Machine
- High-Speed Feeders: Efficiently deliver Sleeves to the inspection station.
- Industrial Cameras: Capture high-resolution images of Sleeves from multiple angles.
- Image Processing Software: Analyzes images to identify defects and classify Sleeves.
- Sorting Mechanisms: Accurately separate Sleeves based on inspection results.
Benefits of Automated Sleeves Sorting
- Enhanced Quality Control: Guarantees consistent product quality by eliminating human error.
- Increased Efficiency: Handles high-volume production with unmatched speed.
- Cost Reduction: Minimizes labor costs and reduces scrap rates.
- Improved Traceability: Tracks Sleeves history for quality assurance and compliance.
- Data-Driven Insights: Provides valuable data for process optimization.
Types of Sleeves Inspection Sorting Machines
- Automatic Sleeves Sorting Machine: Handles standard sorting tasks based on size, shape, and material.
- Machine Vision Sleeves Inspection: Employs advanced image processing for detailed defect detection.
- Camera Vision Sleeves Inspection: Utilizes cameras to capture images for analysis.
- High-Speed Sleeves Sorting Equipment: Designed for high-throughput applications in demanding industries.
- Industrial Sleeves Classifier: Categorizes Sleeves based on various parameters for efficient management.
- Quality Control Sleeves Analyzer: In-depth inspection for critical applications requiring stringent standards.
- Defect Detection Machine for Sleeves: Specialized equipment for identifying specific defects.
Applications of Sleeves Inspection Sorting Machines
These machines find applications across diverse industries, including:
- Automotive
- Aerospace
- Construction
- Electronics
- Manufacturing
Conclusion
Sleeves inspection sorting machines are indispensable tools for modern manufacturing. By ensuring Sleeves quality, efficiency, and compliance, they contribute significantly to overall product excellence. As technology continues to advance, we can expect even more sophisticated solutions to emerge in this field.
[Insert relevant images and videos of Sleeves inspection sorting machines
Would you like to delve deeper into a specific aspect of Sleeves inspection sorting machines, such as the technology behind image processing or the benefits for a particular industry?
Would you like to explore case studies of companies that have successfully implemented these machines?
Let me know if you have any other questions. for information visit https://vesindia.org/products/machine-vision-system/vision-optical-measurement-machine-system.aspx