Boost Your Quality Control with Advanced Vision Inspection Measurement Sorting System for Washers
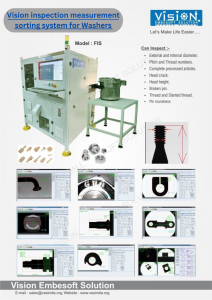
In the fast-paced manufacturing world, quality control plays a pivotal role in ensuring that every product meets stringent standards. When it comes to Washers—bolts, nuts, screws, and other critical components—precision is key. A minor flaw can lead to major issues in assembly, performance, or safety. That’s where advanced inspection and sorting systems come into play. Below, we’ll explore the most effective technologies for ensuring high-quality Washers, utilizing cutting-edge vision, optical, and video inspection systems.
Advanced Vision Inspection Measurement Sorting System Can Inspect:
- External and Internal diameter
- Pitch Detail
- Thread Detail
- Incomplete processed articles
- Slanted Thread
- Reverse Thread
- Pin Roundness
- Length
- Chamfer
- Top, Bottom and Side Inspection
- Presence/Absence Detection
- Defect Detection
- Automated Vision Test and Measurement
- Pattern Matching
- Vision Guided Robot
- Part verification (orientation, function, dimension, finished part features)
- Color Verification
- Barcode Reading & Traceability
- Head crack
- Head height
- Broken pin
1. Vision Inspection Measurement Sorting System for Washers
This system employs high-resolution cameras and software algorithms to inspect Washers for defects such as cracks, surface irregularities, and dimensional inconsistencies. The integrated measurement and sorting capabilities make it an all-in-one solution for manufacturers aiming for flawless production.
2. Optical Inspection and Sorting System for Washers
Optical systems leverage lasers, light sensors, and cameras to precisely measure the geometry of Washers. This allows manufacturers to detect minute discrepancies that might not be visible to the naked eye. By integrating sorting mechanisms, faulty fasteners are automatically separated, streamlining the entire quality control process.
3. Vision Inspection Measurement System for Washers
This system focuses specifically on measuring the dimensions and structural integrity of Washers. It’s a vital tool for ensuring that parts meet the exact specifications required by industries like automotive, aerospace, and electronics, where precision is critical.
4. Optical Inspection Measurement System for Washers
Optical inspection measurement systems are ideal for ensuring Washers are free from defects like burrs, scratches, or deformations. These systems use cutting-edge technology to deliver fast, accurate results, helping manufacturers maintain high production standards.
5. Video Inspection Measurement Sorting System for Washers
By combining video technology with measurement tools, this system provides real-time analysis of Washers during production. The sorting capability allows for the immediate removal of defective parts, ensuring that only high-quality Washers move forward in the production line.
6. Digital Video Sorting and Measurement System for Washers
With the rise of Industry 4.0, digital video systems offer advanced sorting and measurement for Washers. These systems provide enhanced accuracy and speed, offering manufacturers a high-tech solution to manage large volumes without compromising on quality.
7. Video Inspection Measurement System for Washers
This system focuses on using video imaging to measure and inspect Washers. It’s highly effective for detecting defects like dimensional errors or surface irregularities, and it can be integrated with robotic systems for automated quality control.
8. Digital Video Inspection System for Washers
Digital video systems provide a modern approach to Washer inspection, offering real-time, high-definition imaging that makes even the smallest defects easy to spot. These systems are indispensable for manufacturers dealing with high-speed production lines.
9. Camera Inspection Measurement Sorting System for Washers
Using advanced camera technology, this system ensures Washers meet precise measurements. Integrated sorting functions help streamline the manufacturing process by automatically filtering out defective Washers.
10. Imaging-Based Sorting and Measurement System for Washers
These systems use imaging technology to assess the quality of Washers, detecting even the most subtle imperfections. Paired with sorting capabilities, manufacturers can ensure only perfect Washers reach the next stage of production.
11. Camera Inspection Measurement System for Washers
High-definition cameras paired with measurement software provide fast, accurate inspection of fasteners. This system is particularly effective for high-volume production environments, ensuring every fastener is up to standard.
12. Imaging-Based Inspection System for Washers
Imaging-based inspection systems offer a non-contact method to evaluate Washers. They provide high-resolution images that allow for the detection of even the smallest defects, making them essential for industries that require extremely high-quality components.
For more details visit https://vesindia.org/products/machine-vision-system/fasteners-inspection-machine.aspx